Mastering Light Weight Aluminum Casting: a Deep Dive Into the Various Techniques Readily Available
Light weight aluminum casting stands as a keystone of modern-day production processes, offering convenience and precision in creating functional parts and detailed styles. As industries significantly turn to light weight aluminum for its lightweight yet long lasting buildings, understanding the numerous casting techniques comes to be critical. From the traditional technique of sand casting to the facility processes of financial investment casting and die spreading, each technique offers special difficulties and benefits. Comprehending the subtleties of these techniques is essential for ensuring the top quality and efficiency of the spreading procedure. In this expedition of aluminum spreading techniques, we will certainly clarify the details of each technique, providing insights that can revolutionize your strategy to aluminum spreading.

Sand Casting Technique Overview
The Sand Spreading method's flexibility and widespread application make it a keystone in mastering light weight aluminum casting procedures. This method involves creating a mold and mildew from a blend of sand and a binder, such as clay, to form detailed forms for casting molten light weight aluminum. Sand casting is a popular option as a result of its fairly low expense, ease of alteration, and capacity to produce intricate geometries with high accuracy.
The process starts with the production of a pattern, usually made of timber or metal, which is pressed into the sand to produce a mold and mildew tooth cavity. As soon as the pattern is removed, the mold and mildew tooth cavity is full of liquified light weight aluminum, which solidifies to take the form of the pattern. After cooling and solidification, the sand mold is escaped, revealing the aluminum spreading.
Sand casting is commonly made use of in various industries, consisting of auto, aerospace, and manufacturing, because of its adaptability in creating both small and big aluminum components (aluminum casting). Its flexibility to intricate styles and cost-effectiveness make it a recommended selection for several aluminum casting applications
Long-term Mold And Mildew Spreading Refine Explained
Checking out the ins and outs of aluminum casting, the Irreversible Mold and mildew Casting procedure supplies a polished technique for creating top notch parts with accuracy and effectiveness. Unlike sand casting, long-term mold and mildew casting makes use of a multiple-use mold and mildew commonly made of steel or iron to shape the liquified light weight aluminum.
Long-term mold casting can be classified into 2 major types: gravity casting and low-pressure spreading. Gravity casting involves putting the liquified metal into the mold making use of gravity, while low-pressure spreading utilizes reduced pressure to fill the mold and mildew dental caries. Both techniques offer advantages in terms of reducing porosity and boosting mechanical residential properties.
Die Casting: Benefits and Downsides
Grasping the intricacies of die spreading involves understanding its distinctive advantages and disadvantages in the world of light weight aluminum component manufacturing. Die casting deals a number of benefits that make it a popular selection for creating light weight aluminum parts. One key benefit is the high-speed production ability of die spreading, allowing for the mass manufacturing of complicated forms with tight tolerances. Additionally, pass away her comment is here casting offers superb dimensional accuracy and smooth surface area finishes, reducing the requirement for added machining processes. The process is additionally very repeatable, making sure regular quality throughout huge manufacturing runs.
Nevertheless, die casting does include its very own collection of downsides. One significant disadvantage is the high preliminary tooling price related to producing the passes away made use of while doing so (aluminum casting). These molds can be expensive to create, making pass away casting much less affordable for tiny manufacturing runs. In addition, the process is not as flexible when it concerns design changes contrasted to other casting methods like sand casting. In spite of these Click This Link limitations, the advantages of die casting frequently exceed the drawbacks, making it a recommended choice for many light weight aluminum spreading applications.
Investment Casting Applications and Benefits
Structure on the advantages of die spreading, financial investment casting supplies a flexible method for producing intricate aluminum parts with distinct advantages in different applications. Investment casting, additionally understood as lost-wax casting, masters developing intricate shapes that would certainly be tough or impossible to achieve with other approaches. This technique is commonly used in sectors such as aerospace, automobile, and precious jewelry making.
One of the essential advantages of investment spreading is its ability to generate near-net shape components, decreasing the requirement for added machining and minimizing material waste. This leads to price savings and faster manufacturing times compared to traditional machining processes. In addition, investment casting permits the production of get rid of superb surface finishes and limited tolerances.
In the aerospace sector, investment casting is preferred for its capacity to produce light-weight yet solid components important for airplane performance. The vehicle sector benefits from investment spreading for generating components with high dimensional precision and detailed designs. In general, investment spreading supplies a accurate and economical option for making intricate aluminum parts across different industries.

Lost Foam Casting: Just How It Functions
Shed foam casting, also called evaporative-pattern casting, is an approach for producing elaborate steel elements by utilizing foam patterns that evaporate throughout the spreading process. This method starts with a foam pattern of the preferred component being placed into unbonded have a peek at this website sand. The foam pattern is typically covered with a refractory product to enhance the surface area finish of the last metal part. When liquified metal is put into the mold and mildew, the foam evaporates because of the warmth, leaving a cavity that is then loaded by the metal.
One of the vital advantages of shed foam spreading is its ability to produce complicated shapes with elaborate details that might be testing to attain with other casting approaches. In addition, the procedure can be economical as it removes the demand for cores and enables the debt consolidation of numerous components into a single component. It calls for mindful control of the process parameters to guarantee appropriate foam vaporization and metal flow.
Final Thought
In final thought, mastering aluminum casting involves understanding and utilizing numerous strategies such as sand spreading, long-term mold casting, pass away spreading, investment casting, and lost foam spreading. Each strategy has its own advantages and applications in the production process. By familiarizing oneself with these various approaches, makers can select the most suitable spreading method for their specific demands and demands, inevitably bring about reliable and effective production of light weight aluminum parts.
From the standard method of sand spreading to the complex procedures of financial investment casting and pass away casting, each technique provides unique challenges and benefits. In this exploration of light weight aluminum casting methods, we will lose light on the complexities of each approach, offering understandings that might transform your technique to aluminum spreading.
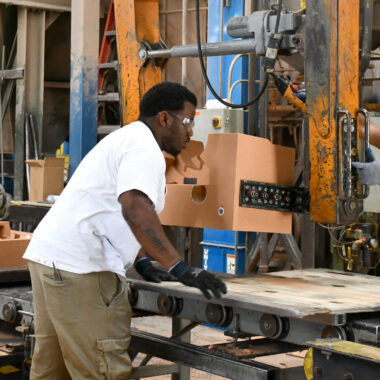